Precision.
Innovation.
Quality.Our Standards
Quality management has been an essential core area at all levels of the company since its foundation. All PAYER employees have the aspiration to develop and produce high-quality products and thus to meet customer requirements for 100%.
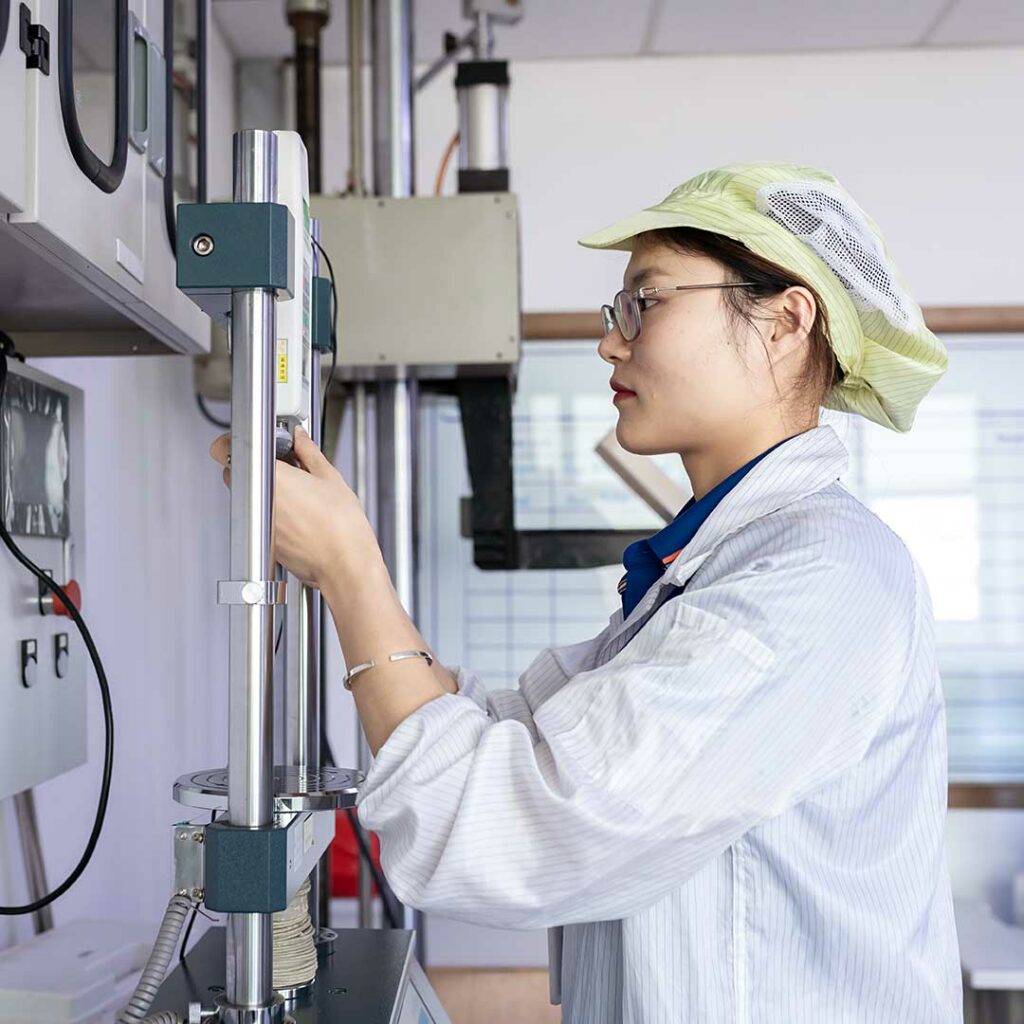
Quality Management
We aim optimal quality on all levels of our business activity in order to reach utmost satisfaction of our partners. In order to be the trusted source of our partners, we strive for 100% process reliability, accuracy and exact documentation of the workflows.
Our development and product locations in Austria, Hungary and China operate according to standards like ISO 9001, ISO 13485, ISO 14001 and ISO 45001. Therefore, we meet all requirements concerning the production of the devices and components for our business areas. In addition to recertifications by accredited external bodies, customer audits are carried out on a regular basis in order to constantly ensure customer satisfaction. Comprehensive product lifetime tests are also part of our holistic quality-first approach.
Due to regular reviews, a high-level quality management can be enabled. Trained staff is responsible for ensuring that these quality management systems are continuously developed and improved.
Quality Policy
In 1946, Eduard Payer founded our company with the ambitious vision: to develop and produce the world’s best shaver for men. Today, as PAYER Group supplies a broad and diverse range of high-quality products and services around the world, we equally try to be the best in everything we do, and we do it as one company. Due to that, each and every one of us is responsible for the highest quality in everything we do. Our vision is therefore very clear: ONE PAYER TO BE NUMBER ONE!
Customer Satisfaction
- It is our basic strategic principle to build a cooperative and sustainable relationship with our business partners based on trust, respect and fairness.
- We are committed to set the requirements of our customers as a standard for the quality of our actions, products and services and also to exceed these expectations.
Operational Excellence
- Maintaining high quality of products and processes as well as striving for improvement, thereby avoiding risks, drive us.
- The zero-defect strategy is our guiding principle at all levels of our company.
- It is our passion to set high and ambitious goals at all levels of our company.
Continuous Improvement
- All employees of the company contribute to the implementation of customer requirements and the realization of the quality policy through their daily actions.
- By taking initiatives, we ensure sustainable positive results for our company.
- Driving continuous improvement and innovation are basic principles of our way of working in order to exceed our own expectations and to satisfy all our partners.
Compliance
- It is our duty to comply with and achieve the policies and processes applicable to PAYER based on requirements of international legislations and standards.
- The maintenance and further development of the quality management system and its successful certification are essential components of our corporate philosophy.
Laboratory & Testing
Using the latest test and inspection equipment, tests are performed on components and processes in our supervised Laboratories & InLine Testing Areas.
Among others, the following test methods are used:
Extract of our equipment:
- 3D Optical Profilometer (Keyence VR-6000 Series)
- 3D Measuring Instrument Dimensional Accuracy & Surface Finish Measurement (Alicona InfiniteFocus G6)
- Digital Microscope (Keyence VHX Series)
- Image Dimension Measurement System (Keyence IM Series)
- Coordinate Measuring Machines (ZEISS CONTURA | ZEISS DURAMAX | MAHR Vision)
- Static Materials Testing Machines (Zwick/Roell Zwicki Line up to 2,5kN)
- Vickers Universal Laboratory Hardness Tester (DuraScan 10/20 G5 | Vickers, Knoop, Brinell 0,00025 – 62,5 kg)
- Cutting Performance Test Machine (Automated Inspection of Cutting Edge – Custom Build)
- Several Custom Build Test Equipment (Tightness | Flow Rate Measurement | Force | Torque | Amplitude | Lifecycle Testing)
- Several Standard Test Equipment (Calipers | Digital Height Gauge| Micrometers | ATEQ | HightSpeedCam …)
Qualification
& Validation Approach
The qualification of equipment and the validation of processes is a central element of regulatory and customer requirements.
Our process describes the procedure and responsibilities for the qualification and validation of our equipment and processes, which have been classified within our risk assessment. It covers all processes from goods receipt to ready-for-sale goods.
Validation is the documented evidence that these processes consistently produce a result or product that meets the defined specifications.
Together with careful product design and process design, it ensures reliable compliance with the defined specifications and consistent product quality.
We have developed this approach, follow it and also continuously adjust it to achieve the following goals:
- Ensuring high process capability
- Ensuring a high level of process reliability
- Compliance with regulatory requirements
- Meeting or even exceeding customer requirements
- Conservation of resources
- Contribution to a sustainable environment
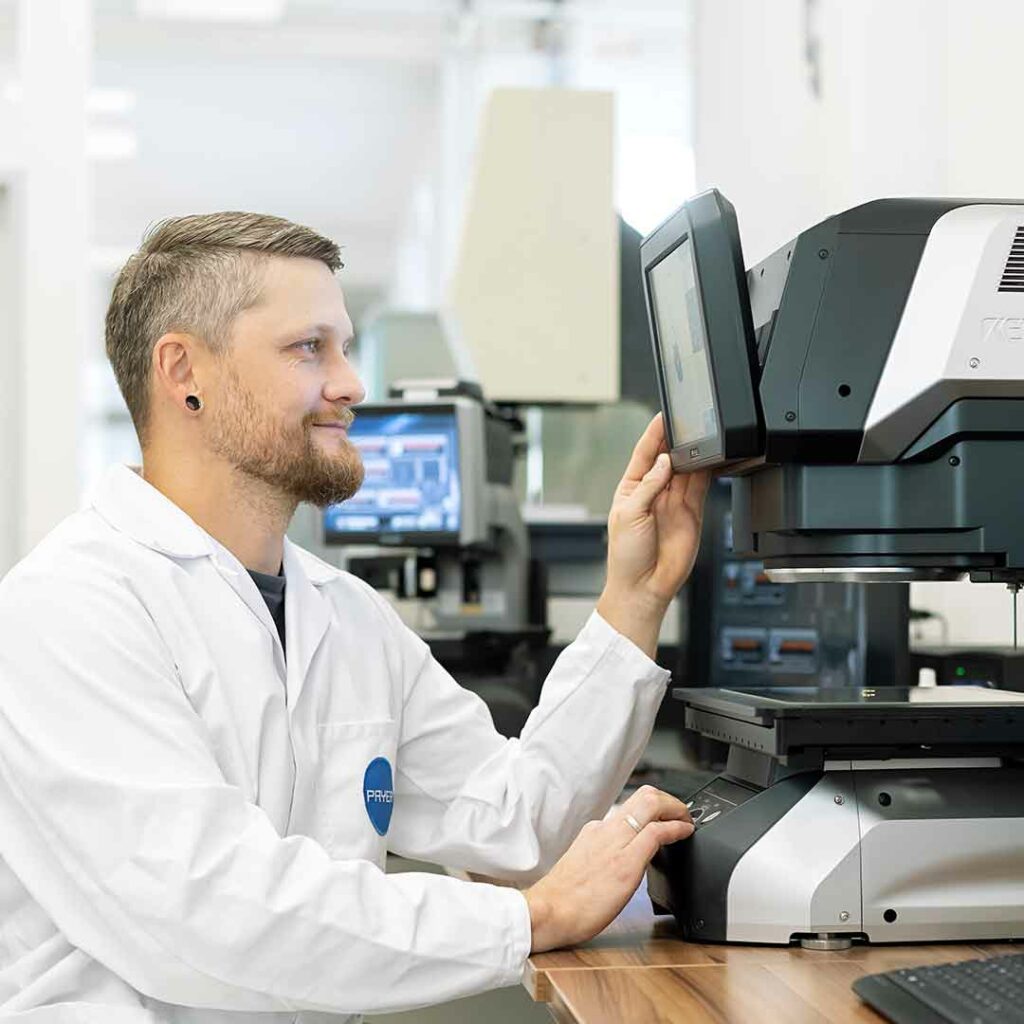
Our certifications can be downloaded subsequently:
PAYER Austria
PAYER Malaysia